Fabrication of aluminum flake powder by the wet ball milling of aluminum foil scraps and the effect of related factors were studied. As foil thickness decreases from 60 to 6.5 mm, mean size of powder milled for 30 h decreases from 107 to 17 mm. It is impossible to mill the foil without oleic acid to fabricate the flake powder. As content of oleic acid increases from 1.5% to 5%, mean size of flake powder milled for 30 h is drastically decreased. For the mineral spirits content below 50%, foil scrap was not fragmented because balls coated by oleic acid were slid in the jar by reduced friction. As weight ratio of mineral spirits to foil increases over 100%, foils were milled to powders with mean powder size 15–20 mm irrespective of mineral spirits content due to reduced lubricant effect. The result of the painting test shows that the content of aluminum flake powder in paint greatly affects the degree of gloss of painted automobile body.
Introduction
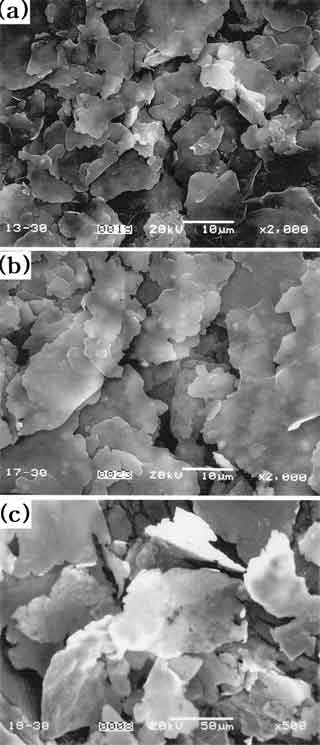
wet ball milling process
A considerable amount of aluminum foil scrap has been produced by slitting of aluminum foil that was obtained by rolling of aluminum, and great attention has been paid to recycling of foil scrap. For thin thickness Ž6–120 mm. and high purity of over 99.4%, the scraped aluminum has a great potential as a raw material to fabricate aluminum flake powder by mechanical grinding. Aluminum flake powders have been widely used in fingerprint detection, aerated lightweight concrete, as a paint component for automobile and industrial applications, an additive for ink, and explosives due to their metallic color, glossy appearance and good adherence w1–8x. The aluminum flake powders of mean size 20–45 mm and water covering area of 4000–30,000 cm2rg are mainly used in the industry w2x. In paste manufacturing industry for paints and inks, flake powders are produced by the wet ball milling process of gas atomized aluminum powder. The wet ball milling is performed in inorganic solvent such as mineral spirits w3,4x.
In this study, the milling behavior of aluminum foil scrap for producing the flake powder was investigated. The effects of factors related to the milling process such as initial foil thickness, milling time, oleic acid content, ball size, and weight ratio of mineral spirits to foil were also studied. The painting tests were performed to check one of the possible applications of aluminum flake powder that was prepared by the wet milling of aluminum foil scrap.
Experimental procedures
The aluminum foil scraps of various thickness Ž6.5, 16, 60 and 120 mm., 8 mm in width and purity of 99.4 wt.% were cut into chips of size below 5 mm by rotary type blades. Aluminum foil scraps of 10 g, 725 g of stainless steel ball with diameter of 16 mm, 3 wt.% of oleic acid as milling agent and mineral spirits of 10 g were charged in the horizontal stainless steel container of length 80 mm and inner diameter of 70 mm. The milling was performed for 60 h under rotation speed of 120 rpm, which was 78% of critical revolutions per minute w7–9x. The main variable parameters in wet ball milling process were the initial foil thickness Ž6.5, 16, 60 and 120 mm., the content of oleic acid Ž0%, 1.5%, 3% and 5%., the weight ratio of mineral spirits to foil Ž0%, 50%, 100%, 200% and 300%., and ball size Ž16 and 4.8 mm.. These parameters were varied in order to investigate their effects.
The mean size and water covering area of powders were measured by the particle size analyzer ŽCoulter LS130. and DIN standard 55923, respectively w10x. Water covering area of flake powder was defined by water covered area per gram of aluminum powders coated by isobutyl alcohol after cleaning by acetone. Thickness and aspect ratio of aluminum powder were calculated according to the formulas of 1rŽAl density 2.7 grcm3=water covering area. and mean powder sizerthickness, respectively. The shapes of aluminum flake powders were also observed by scanning electron microscopy ŽSEM.. Paints containing aluminum powders with different powder size were prepared by mixing of aluminum paste 3.8%, thinner 24.2% and lacquers 72%. Then, the glass plates were painted by these mixtures. On the other hand, aluminum paints of different Al paste content under constant ratio Ž1:3. of thinner and lacquers were also prepared and painted on basecoated automobile body in order to check the effect of powder amount on the degree of gloss. The degree of gloss was measured by Horiba IG-320 608 Gloss checker.
Results and discussion
Fig. 1 shows milling time dependencies of mean powder size for the foils with different initial thickness. In spite of milling of up to 60 h, it is still difficult to make flake powder by ball milling of foils with 120 mm in thickness. The foil scraps with initial thickness of 60 and 16 mm are not changed into powders by milling for 15 h; however, the flake powders with mean powder size of 107 and 25 mm could be obtained by milling for 30 h, respectively. The powder size continuously decreases by milling for 45 h. In contrast with foil scraps with initial thickness of 60 and 16 mm, the one with initial thickness of 6.5 mm was changed into powders of 20 mm in mean size by milling for 15 h. This means that thinner foils are easy to be plastically deformed and fractured into fine flake powders by impact force of falling balls.
Fig. 2 shows microstructures of aluminum flake powders prepared by milling of foil scraps with different initial foil thickness for 30 h. In comparison to the foil scrap with initial thickness 60 mm, the one with 6.5 mm in thickness was milled to finer flake powder. Water covering area, flake thickness and aspect ratio of flake powder vs. milling time are presented in Fig. 3. Water covering area of flake powder is increased with milling time due to the increase of specific surface area of milled powder. Flake thickness of powder is decreased continuously by milling up to 30 h. For the foil of 6.5 mm in thickness, as milling time increases to 30 h, aspect ratio of flake powder is increased to maximum due to high degree of flake. After milling for 60 h, flake powder is fragmented into fine powder with low degree of flake.
Fig. 4 shows the mean size of powders milled for 30 h with the different weight ratio of mineral spirits to foil. For the mineral spirit content below 50%, foil scrap with initial thickness of 6.5 mm was not milled because of sliding motion of balls coated by oleic acid. As weight ratio of mineral spirit to foil increases over 100%, foils were milled to powders with mean powder size of 15–20 mm irrespective of mineral spirit content due to reduced lubricant effect. After milling for 30 h, content of mineral spirits in aluminum paste was controlled as 35% below by vacuum drying for pigment application.
Oleic acid is usually added to aluminum paste for controlling non-leafing character and milling behavior. Effect of oleic acid on mean size of milled powder is shown in Fig. 5. It is impossible to mill the foil without oleic acid to produce powder due to coagulation of foils. As content of oleic acid increases from 1.5% to 5%, mean size of powder milled for 30 h is decreased drastically due to prevention of coagulation as shown in Fig. 6.
Fig. 7 shows the variation of mean powder size with milling time in the case of using balls of different sizes. After milling for 60 h, using 16-mm diameter balls, the mean powder size is slightly smaller than that for the smaller balls. This means that the larger balls give more impact force to the aluminum foil than the smaller ball in spite of a small collision frequency.
The degree of gloss after coating with paints containing 3.8% of aluminum paste prepared by milling for 15, 45 and 60 h with 6.5 mm foil are 28.4, 26.7 and 25.8 on base of 100 in the case of glass plate, respectively. The decrease of gloss with milling time is due to diminution of specular reflection of light by fine powders. On the other hand, when aluminum paints with various content of paste were painted on base-coated automobile body, the variation of degree of gloss was shown in Fig. 8. As aluminum paste content in paint increases from 0% to 5%, the degree of gloss increases from 15.7 to 24 due to hiding of dark base-coated body and high reflectivity of aluminum flake powder in coated layer. Too high aluminum paste content in paint up to 15.3% drastically decreases the degree of gloss as too many aluminum flake powders reflect the light diffusely. Thus, 3.8–5% of aluminum paste in paint was verified as the optimum content. Also, the appearance of the automobile body painted with a paint containing aluminum paste was good, suggesting that the aluminum paste prepared by a milling of foil scrap can be used as a pigment for car paint.