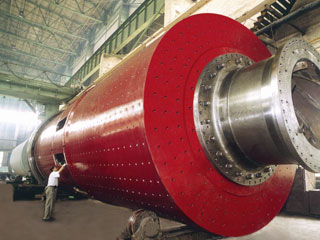
Vertical Ball Mill Slakers
The question most often asked is “What is the best type of slaker?” The answer to this question is often complex and depends on factors such as:
- End use of produced lime slurry
- Type of quicklime used
- Quality of slaking water
- Quantity of lime slurry required
- Quality level of produced lime slurry required
To address the above, let us first review the types of slakers available in the marketplace today.
A. Detention or Slurry Slakers
B. Paste Slakers
C. Batch Slakers
D. Horizontal Ball Mill Slakers
E. Vertical Ball Mill Slakers
The following pages will describe each type of slaker with their advantages and disadvantages.
Horizontal Ball Mill Slakers
Standard Horizontal Ball Mills are sometimes used for lime slaking. Considering that Ball Mills are designed for grinding, and the slaking process is simply a chemical process, it is obvious that the use of a Ball Mill for slaking is not the best choice of equipment in most cases. However, there are a few cases where the use of a Ball Mill slaker is advantageous. These include:
- When the slaking water sulphates or sulphites content is more than 500 PPM, the sulphates or sulphites coat the pebbles of quicklime and prevent water from reacting with the lime. The only way this reaction can take place is the outer layer that is covered with the sulphate must be abraded away to allow water to penetrate lime pebbles. The only slaking equipment that can achieve this efficiently is a Ball Mill slaker.
- In the case of the water with low sulphates or sulphites, the ball is used only to grind 5%of the total feed which is grit. This certainly is a very expensive way to get rid of 5%grit. In addition, since the entire body of the mill plus the media has to be rotated, it requires many times more power than the conventional Detention or Paste slakers.
- In applications where magnesium lime is to be used in place of calcium lime, slaking this type of lime is very difficult in regular slakers if pebble dolomitic lime is used. With pebble dolomitic lime, slaking can take place only under high pressure and high temperature. In Detention type slakers, only pulverized dolomitic lime can be slaked at temperatures near 200°F and a residence time of about 30 minutes. The Ball Mill slakers can be effectively used for slaking dolomitic pebble lime, since pebbles will be ground to a fine particle size. The mill temperature for slaking dolomitic pebble lime should be about 200°F. With this high temperature, special mill lining must be used. The normal mill rubber line will deteriorate at this temperature.
- Detention type slakers are typically made with a maximum feed rate of 20 tons per hour. The Horizontal Ball Mills can handle capacities much larger than 20 tons per hour. However, from the economic point of view, using multiple Detention slakers to get the maximum capacity is generally much less expensive.
Vertical Ball Mill Slakers
There are two types of Vertical Ball Mills on the market:
1. Vertical mill 2. Attritor Ball Mill
Both mills have stationary bodies and moving shaft and media. The difference is how the media is energized to move.
- In the Vertical mill the media rises by a vertical screw and falls by gravity on the outer circumference of the screw. In this machine, the drive energy is used only to raise the media not to grind. The grinding is done by the gravity fall of the media and its impact to the other media during the gravity fall. Since media has to fall by gravity, the media has to be large enough in size to crush the lime particles as well as grit. Media in this mill is 1″ and 1-1/2″ diameter. The Vertical mill sketch shown here is a Gulin Mineral Vertical mill.
- In the Attritor Ball Mill, the media is agitated via a shaft with multiple arms. The shaft rotates at a speed to create an arm-tip speed of about 1, 000 feet per minute. The agitated arms impact the media and throw the media in all directions in a random pattern. The lime and grit are impacted by energized media and are ground by a shear as well as impact. The media in this type of mill is generally 5/16″ 1/2″.