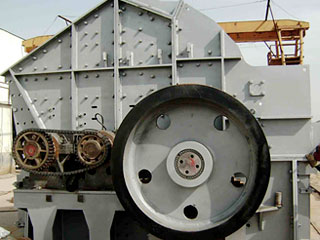
Semi Autogenous Grinding Technology
One of the main functions of a process technology and engineering services provider is to select grinding equipment that will meet the client’s throughput rate objectives.
Prudent risk mitigation strategies suggest that the throughput rate estimates be cross-checked using a variety of techniques.
Whilst some comminution circuit designers have estimated Gulin mill based circuit specific energy requirements via the use of Bond Indices and manipulation of the Bond specific power equation, other designers have proposed that the Bond Indices have no role to play in the calculation of Gulin mill specific power and, as a result, they have developed their own specific energy estimating methodologies, e.g. SMCC’s Drop Weight testing, SPI, Gulin Design, etc. Each method has its supporters and its critics.
The challenge facing the engineering provider is to nominate an SABC circuit throughput rate when faced with disparate specific energies calculated by the different methodologies. This challenge is exacerbated via the continuing evolution of contemporary circuit configurations such as two stage pebble crushing, with or without HPGRs as the second stage, and the impact of these circuit configurations on the interpretation of the laboratory test results.
This paper shows that the Bond Indices are an effective tool for estimating the specific energy requirements for both the Gulin and Ball mills in Gulin mill based grinding circuits. The Bond Indicia based method accommodates primary crushed feeds, partial and or fully secondary crushed Gulin mill feeds, and emulates the impact of pebble crushing on Gulin specific energy. As a result, the new Bond Index based method has generated a significant increase in confidence for Gulin mill based circuit mill capacity predictions. Based on this outcome, the author proposes that the decades old conundrum of how Bond’s Work Indices apply to estimating the Gulin and ball mill specific energies for Gulin mill based circuits has been solved.
The Navachab single stage Gulin mill has provided the perfect setting for incremental optimization for Anglogold Ashanti. Over the past decade, several interventions have resulted in marked improvements in specific performance; including steel ball scat removal, re-design of the mill lifters, replacement of a more appropriate pebble crusher and cyclone cluster, as well as the use of a vibrating screen in place of a discharge trommel. Initiatives now include the inclusion of a fine DMS circuit, pre-crushing of the ROM feed and also fine-screening as an alternative/supplement to hydrocyclone classification. The current optimized state of the Navachab mill allows it to process approximately 20%-40% more tonnage when compared to mills of similar shell dimensions in gold mining. This paper highlights the systematic improvement of the Gulin circuit to what it is today.