Introduction
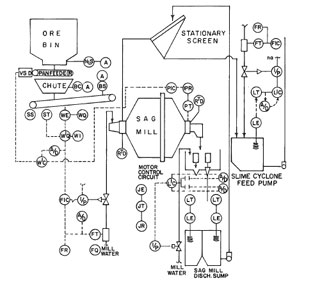
Semi-autogenous Grinding Mill
Benguet CorpDratiDn’s Kaline Concentrator treats about 19000 t! d of. ore containing 0, 45% copper and 1, 0 g Ault. Eighty-five percent. of the copper and 65%. of the gold are recDvered in a concentrate assaying 21 070 CDpper which is shipped tD smelters in Japan and in the Philippines. The ore body is a small porphyry-type depDsit with grindability ranging frDm a BDnd work index of 8, for soft clayey ores, tD 20 kwH/t fDr the very hard metavDlcanics. Clay content varies frDm 10 tD 35%. Because of this clay, semi-autogenDus grinding of broken run-of-mine. ore is employed instead-Df conventiDnal crushing and grinding. The semi-autogenDus mill acts as the ‘crusher’ and scrubber.
The mine and mill are located 250 km northwest of Manila, Philippines. The property is owne4 by the DizDn Copper-Silver Mines, Inc. and is. operated and managed by Benguet CDrpDration. Operations began in 1980. It has been profitable ever since, despite depressed metal prices in 1984 and 1985, mainly because of exceptional gold in the ore.
Semi-autogenous grinding circuit
The grinding circuit was. originally designed to process 1700011 d. on a on-line semi-autDgenDus/ball mill grinding circuit. Subsequent imprDvements have increased capacity to 19 000 11 d. 2 The circuit is shown in Figure 1.
Ore from the open pit is delivered by 77-tDnne trucks to the dump pDcket. Bouilders that do nDt pass the 610 mm grizzly are crushed by tWD rock breakers. The. ore is then withdrawn frDm the 1700-t bin under the grizzly by a variable-speed pan feeder and is conveyed to the 8, 54 m diameter by 4, 12 m long dDminion semiautogenous grinding mill. on an 1 828 mm belt CDnveYDr. The mill is driven by tWD 3 000-HP motors through gear reducers resulting in a total connected hDrsepDwer. of 6000. Semi-autDgenous mill speed is 10, 7 rpm, . or 73% of critical. The mill is loaded with 100/0 by volume of 100 and 125 mm forged steel grinding balls. Ground material discharges into a sump and is pumped to a stationary screen with 12, 7 mm opening. The undersize materials drop to a cyclone feed sump while the oversize gravitates back into the semi-autogenous mill.
Screen undersize is pumped by a 355 mm X 305 mm slurry pump to a cluster of eight radially mounted D-26 Krebs slime cyclones, with the overflow going directly to the slime rougher flotation circuit. Cyclone underflow provides feed to the 5, 03 m diameter x 8, 54 m long overflow Dominion ball mill that operates at 14, 2 rpm or 73% of critical. The ball mill uses two 3 ODD-HP synchronous motors. The ball mill discharges its product into a sump from where it is pumped by a 508 mm X 457 mm slurry pump into a cluster of eight D-26 Krebs sand cyclones. The overflow goes to the sand rougher flotation circuit and the underflow goes back into the ball mill.
Instrumentation as originally designed (Figure 2) included an analogue horsepower control loop for the semiautogenous mill circuit and a water-to-ore ratio controller. The wide variation in grindability, however, caused tonnage variations of 450 to over 1 100 tlh. This adversely affected the control of downstream operations thereby forcing the operators to switch frequently from automatic control to manual control. Capacity was not maximized under manual control because operators were reluctant to load the mill to higher levels of power draw, since an abrupt increase in ore hardness could cause a mill overload.
A 64 k-byte FOX-3 Foxboro process computer was also part of the original instrumentation, but the computer was used mainly for monitoring and reporting. It was recognized that a more sophisticated control system using the capabilities of the computer was necessary to maximize the capacity of the semi-autogenous mill while at the same time preventing fluctuations in the feed rate. This was particularly important whenever treating hard and finely fragmented feed that lacked competent rocks as grinding media. The initial computer control scheme, which essentially duplicated the analogue control scheme already installed on the mill, was also not applicable.
Control scheme
Except on hard and finely fragmented ores where throughput is too low, the control strategy is to maintain a constant tonnage at a level not to exceed the capacities of the ball mill, pumps, cyclones and flotation cells. The control instrumentation associated with this control scheme is as follows:
- A weight transmitter to measure new feed rate, and a variable speed pan feeder for controlling feed rate.
- A flow transmitter for headwater flow rate measurement and pneumatically operated butterfly valves’for flow control.
- Semi-autogenous mill horsepower and bearing pressure transmitters to infer the mill load.
- An ultrasonic level transmitter to measure sump level
The mill discharge sump level is controlled by sump water addition. New feed rate is cascade-controlled by. the power draw. Water to the head of the mill is adjusted according to the set water-to-new feed ratio. All controllers are standard proportional plus integral analogue controllers with manual, automatic and direct-digital facilities.
The above system suffered from a number of problems, the most serious of which was on changes of ore hardness. The wide variations in feed rate that resulted caused erratic control of the ball mill, cyclones and flotation machines.
It was also difficult to maintain the grinding density at optimum level. The objectives for the computerization of the control scheme were thus addressed to the following two factors: maintaining power draw at a high but stable level using small changes in feed rate so as not to upset downstream operations; and optimizing of the grinding density. To attain this, a visor-type computer program that would determine and adjust the set points of the controllers was developed.
Computer program
With the operator-directed automatic control, the semiautogenous grinding mill can be operated very close to maximum capacity without upsetting downstream operations provided it is very closely vised. Instead of an operator, a computer program that ‘vises’ the process was developed based on a study of how operators responded to changes in the ore’s grindability. The computer program was designed to increase the feed rate set point at 1 percent increments if after 2 minutes the following conditions were met:
- the power draw was below critical,
- the power draw was stable or decreasing during the previous 2 minutes,
- the bearing pressure was stable or decreasing during the previous 2 minutes.
Water to the head of the mill was adjusted (water-tofeed ratio) to the feed rate set point to keep the grinding density fairly constant.
When any or a combination of the three aforementioned conditions was not met, the feed rate set point was either maintained or reduced in small increments depending on the level of the power draw and bearing pressure, and the rate at which the power draw and bearing pressure were changing. Fast downward changes in feed rate were only made when an impending overload was detected by the computer.
In this manner, the mill is operated at a high but stable power draw without wide fluctuations in feed rate. The feed rate control principle is shown in Figure 3. Headwater is similarly controlled. Every 14 minutes the water-to-ore ratio was changed and the effect on power draw and bearing pressure determined. If both the power draw and bearing pressure had decreased after the change in the set point, the new water-to-ore ratio was maintained for the next 14 minutes. If either the power draw or the bearing pressure increased, then the previous ratio was maintained; but if both variables increased, then the direction of the change in the ratio was reversed. In this way, grinding density was kept close to optimum.
System evaluation
Table 1 gives a comparison of the results achieved before and after implementing computer control on a hard, finely fragmented ore.
With the installation of computer control, the variability in the control of power draw improved from a variance of 90 hp under the operator-directed automatic control mode to 31 hp. Owing to this reduction in control variability, capacity has increased by 3070 on hard, finely fragmented ores, when the system is used. This occurs about 30% of the time. Basing calculations of the economic return on this increase and at 30% utilization, additional net revenue generated by the control system is calculated at $0, 05 per tonne. This is equivalent to almost $0, 4 million per year.
Conclusions
The visor-type control scheme described here has provided significant gains in semi-autogenous grinding mill throughput without upsetting subsequent operations. Since the control scheme was patterned after the operatordirected automatic control mode, it is easily understood by the operators, and this has contributed to its success.