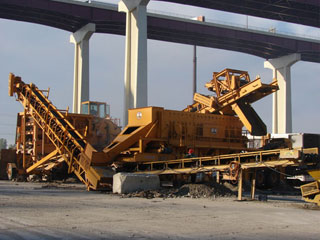
Peripheral System Design
Limestone Storage & Handling
The moisture content of the stone can be controlled some- what by the upstream handling system design. Covered stor- age, protecting against direct rainfall, can prove economical if significant drying and/or handling system costs are saved. Pur- chasing larger ‘run-of-crusher’ stone can reduce the moisture levels in the limestone, as the maximum amount of moisture bulk stone can contain is a function of the fines content. Larger stone sizes with less surface area allow for more natural drain- ing and reduced moisture content. The drawback is the need for an additional pre-crusher. However, pre-crushing operations can improve overall energy efficiency and apply well to the tower mill and attrition mill system designs.
The storage requirements for the ground product can impact the system design capital costs, energy consumption and arrange- ments.
One cubic foot of limestone slurry at 30%suspended solids weighs approximately 77 pounds and contains only 23 pounds of limestone. Whereas, one cubic foot of 3/4”x 0”stone weights about 90 pounds and contains 90 pounds of limestone. This re- iterates the knowledge that dry storage is more efficient use of storage volume compared to that with a wet milled product.
A multiple attrition mill system can be more ideally suited to system designs where the limestone is bulk stored on the ground and reclaimed to individual surge bins upstream of each mill. However, incorporation of larger day silos it certainly pos- sible as it is with the typical horizontal ball mill system.
In general, the entire system from limestone unloading to the final milled product should be evaluated to ensure possible synergies are identified and taken advantage of. In this man- ner, the overall plant storage, processing efficiency and reli- ability are maximized.
Absorber System Design
Absorber designs can be influenced by mill system perfor- mance and operating efficiency. Achieving an equivalent grind with less energy can allow power savings that can be banked or re-allocation elsewhere. Achieving finer grinds at acceptable energy usage can allow tailoring of the grind size to assist in optimization efforts in the wet FGD absorber and dewatering system design.
Wet FGD absorber design often requires the juggling of ab- sorber tank size with limestone dissolution, Ca/S ratio, and gyp- sum precipitation design factors. Fig. 4, provides an indication of how absorber tank size can be influenced by grind size when holding all other factors constant. Taken in isolation, the effect is significant. However, in reality reductions in reaction tank size must be weighed against corresponding influences on the oxidation system design, absorber recirculation pump design, recirculation rates, gypsum precipitation and crystal growth. Yet, even a slight reduction in tank size will translate into capital cost savings. This is especially true if the vessels are constructed of high alloys and/or enclosed in buildings.
With increasing fineness of the limestone grind, classifiers within the dewatering system can more easily produce quality gypsum products while maintaining a higher calcium-to-sulfur stoichiometric ratio within the absorber loop. This improves absorber performance and/or allows similar performance with reductions in tank size or liquid to gas ratios.
From an evaluated power cost alone, the use of more effi- cient limestone grinding techniques can provide for significant savings over the life of the plant. Comparing capital and energy costs throughout the FGD system design scope is simplified by placing the values on a common unit basis. Often the quantity per unit of SO 2 removed is used($/t, kWh/t, etc. ).
A typical ratio of limestone consumption per unit mass of sulfur dioxide removed is approximately 1. 8 grams of limestone per gram of SO 2 removed. Using this factor the mill system ap- plied energy in units of kWh per short ton of dry limestone can be corrected to a unit mass of SO 2 removed basis, rather than a unit mass of limestone ground basis.
Applying this correction, Fig. 5 depicts how the mill system design can influence power costs over a range of power evalu- ation factors.
Plots of this type can help in visualizing where and how to optimize the overall plant design capital versus energy costs the age old plant design optimization problem.
Summary
While the traditional horizontal ball mill has its place in the industry, alternate mill systems are providing competition. With flexible sparing philosophies, the additional equipment required to feed multiple mill systems can be offset by reductions in mill costs and improvements in energy efficiency.
Attrition mills are particularly suited towards this endeavor through their characteristics of compact size and approximate 50%power savings over the traditional horizontal ball mill sys- tem. They represent a prime example of how alternate equip- ment choices can provide for improvements in system design and economics.
In conclusion, when considering non-traditional process equipment, the entire plant site envelope must often be evalu- ated to ensure maximized gains. With this particular subject, the use of smaller efficient attrition mills can offer space, foun- dation and energy savings in the reagent preparation area. Fur- ther more, FGD system design optimization efforts can be en- hanced by providing increased flexibility with regard to final grind size