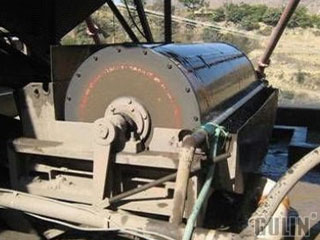
Wet high-intensity electromagnetic separators
The hard rock deposit for Case Study 2 consisted of iron and titanium bearing minerals as well as vanadium and other gangue minerals. The main goal was to recover the abundant magnetite and ilmenite components; however, ilmenite recovery was problematic, hovering in the 17–20% range, because sufficient technology for recovery of the significant values in the -45 μm fraction was not initially available.
Studies were performed to upgrade the operation. Test work revealed that the recently developed Gulin® Wet high-intensity electromagnetic separators was the key to enabling the operation to process this fine fraction. The plant was upgraded with Gulin® Wet high-intensity electromagnetic separators technology to process the –45 μm stream. The result was an overall doubling of TiO2 recovery at an average concentrate grade of 47.5% TiO2. Additionally beneficial, the Gulin® discarded most of the gangue minerals and slimes prior to flotation so less than one quarter of the initial mass feed entered the flotation circuit.
While the Gulin® application was a great improvement, the tailings still contained approximately 7% TiO2. Further testing led to the implementation of a tailings reprocessing circuit to gain additional recovery. Again, the upgrade employed Gulin® Wet high-intensity electromagnetic separators technology. A simplified flowsheet of the final tailings retreat circuit is shown in Figure 5.
Low-intensity magnetic separators are utilized to recover any remaining magnetite. The LIMS is followed by a rougher stage of two Gulin®-1500 magnetic separators. A third Gulin®-1500 magnetic separator is then applied to recover ilmenite in a cleaning stage.
Combined, the three Gulin®-1500 separators discharge 81.5% of the mass fraction to the final tailings at very low cost, with only 18.50% of the plant head feed moving forward in the process. The tailings retreat circuit produces a product grade of 47.66% TiO2. Recovery of the ilmenite is 31.19%, which equates to an additional 30 000 tons ilmenite concentrate annually for the operation.
Dry magnetic separation was not recommended for this application for the following reasons:
- Flotation is used throughout the initial flowsheet and the tailings retreat circuit, so additional drying costs would be present
- Ultra-fine materials are difficult to process with dry magnetic separation
- No rutile or zircon co-products were present; hence no dry processing was necessary.