Introduction
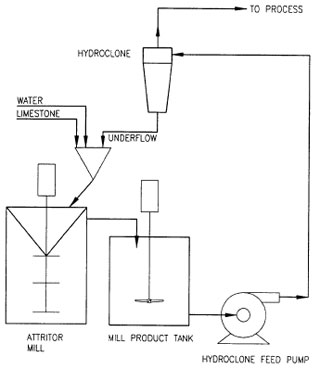
single loop attritor mill grinding system
Horizontal ball mills have dominated as the equipment of choice for limestone grinding functions within wet flue gas desulfurization (WFGD) systems. Recent years have led to a more wide spread investigation and acceptance of alternative mill system designs. Mill types considered within the industry have ranged from a variety of media mills to dry roller mills.
The science and application of size reduction processes is a complex subject. Similarly, the design of the FGD system is also complex and can be influenced by many factors. Determining the most cost effective and energy efficient grinding method for each application can require an exhausting study.
The detailing of optional designs with significant capital cost, power and operational information is time consuming to produce and evaluate.
Presented is a review of limestone grinding for FGD systems, with an attrition mill option exemplifying how advancements in comminution processes influence overall FGD system design. Relative grinding energy efficiencies are presented to assess the impact of operational power consumption and installed power. The goal is to shed light on overall objectives and design path alternatives.
Wet FGD Limestone Grinding
The wet horizontal ball mill has typically been the workhorse for limestone slurry preparation within a wet FGD system. Undoubtedly, the horizontal ball mill has certain characteristics that suit it well to FGD service, these primarily being:
- Wet grinding capability
- Large reduction ratio capability (ability to take a 1″ feed size to a micron range product)
- Resistance to abrasion
- Relatively low operation, control and maintenance requirements
Wet grinding is usually preferred over dry grinding. When looking at the grinding process in isolation, there are pros and cons of wet versus dry. Dry grinding requires more power, yet has less ball and liner consumption that in wet grinding. Additionally, the capacity of a dry mill is typically less per unit mill volume than it is with wet milling.
However, it is the overall FGD system design and use requirements that push the selection in the direction of wet grinding. The two main reasons are that the ground product is utilized in a wet process and that the received condition of the stone can be one of relatively high moisture.
In addition to the higher dry milling energy required, when feed stone surface moisture rises above 2-3% by weight, a heated air source to accommodate drying is typically required. This usually leads to unacceptably high energy costs. Indeed, in most industries, the increased energy consumption and the capital cost of the equipment can swiftly move the overall economics away from dry grinding when a wet slurry is a desired end product.
A commonly specified FGD limestone size for feed to the mill system is 3/4” x 0”. This is a loose description of a size distribution which can be thought of as all of the particles smaller than 3/4” with the distribution extending into a fines range below 20 mesh. Size ranges described in this manner are variable in practice and can have occasional 1 to 3” tramp material and/ or higher percentages of fines. The horizontal ball mill is capable of accepting this stone size direct, without any pre-crushing function, thus improving system flexibility, simplicity and reliability. Abrasion is controlled with wear resistant mill liners and by the inherent concentration of the wear in the media.
Alternative Designs
An alternate wet ball mill design that has gained acceptance in the FGD industry is the tower mill or vertical ball mill.
Vertical ball mills are a form of ‘stirred’ ball mill and can be more energy efficient than typical horizontal ball mills. Their increased efficiency is partially explained by placing the grinding action in solids beds that are of a more optimum thickness or porosity. The variation in the transport of the feed through the mill, the distribution of feed in the ball charge media, and the method of energy transfer to the media are also factors which help explain the difference in efficiencies.
Furthermore, tower mills are typically fed with a 1/4” x 0” feed size. While this necessitates the use of a pre-crusher when a larger sized stone is received, it allows for the mill to be sized for a smaller reduction ratio and a more optimum media charge size distribution.
Wet FGD Limestone Attrition Milling
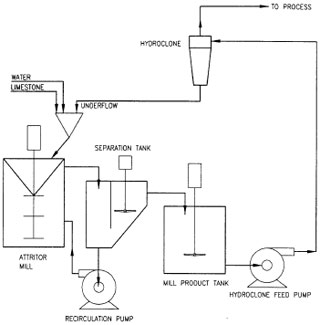
double loop attritor mill grinding system
Attrition milling is another approach beginning to gain acceptance in FGD. Attrition milling is also not new. Various forms of attrition milling have been used across a wide range of industries and applications, such as paints, pigments, pharmaceuticals, ceramics and coal slurries. The attrition mill could be considered on the other end of the loose generic description of stirred media or stirred ball mills. Similarly, some have classified the vertical ball mill as being in the family of attrition mills.
The tailoring of the mill design to the specific application can be critical with attrition mills, as they operate at higher speeds, smaller volumes and higher localized energy concentrations. This mill type was chosen as an example of how mill system advancement, optional mill system arrangements and sparing philosophies can impact overall system design and process effectiveness.
The mill was designed specifically for limestone grinding with a reduction ratio equivalent to that typically applied to the vertical ball mill in FGD service. This is taken to be the comminution of 1/4” x 0” mill feed size to a 95% less than 325 mesh product size. Since the design of the attrition mill is suited to obtaining extremely fine grinding, finer product sizes are possible and are evaluated to some extent later.
The original attrition mill was invented by Dr. Andrew Szegvari in the 1920s. The invention is significant in that it marked the beginnings of agitated media milling. As mentioned earlier, the stirred ball mill term is often used as it depicts a grinding mill which utilizes a stationary vessel and internally agitated balls. The concept is integral to the design of the attrition mill. Power input is used more directly for agitating the media rather than for rotating a large heavy tank and its contents, as in the case with conventional horizontal ball milling.
Optimal fine grinding requires both impact and shearing force. In the mill, the rotation of the horizontal arms directly imparts energy to the grinding media, thus causing the balls to randomly collided with one another. These collisions create the necessary impact forces to break down individual particles in the slurry. In addition to the impact forces of the media, the balls are also spinning in different directions, thereby creating shear forces on the adjacent slurry. The combination of these impact and shearing forces results in efficient size reduction. In 1946, Dr. Szegvari embarked on further development of attrition milling and particle size reduction technology. Today, after more than 50 years of continual research and development, there are many different types of attrition mills used worldwide in various industries and research laboratories.
In 1991, a continuous grinding attrition mill for lime slaking applications was produced. These mills have been successfully applied to dry FGD systems where a slaked lime product is required. Building upon that success, an attrition mill for continuous grinding of limestone was introduced in1996. The mill was specifically designed with increased grinding capability for continuous wet milling of limestone in wet FGD services.
The system has demonstrated efficient processing of limestone from 6mm down to 95% minus 325 mesh on a continual basis. Within the system boundaries are a separation tank, mill circulation pump, mill product tank, hydroclones and hydroclone feed pumps. (Reference Fig. 1 & Fig. 2)
During wet milling of FGD limestone, both limestone and water are continuously fed from the top of the mill through a specially designed feed housing. This funnel shaped housing has a cylindrical extension, which projects into the grinding vessel of the attrition mill. The shaft of the mill extends down through the housing and the cylindrical extension with the media agitator arms being disposed just beneath the extension.The rotating shaft utilizes several radially projecting,angled impel- ler blades,which are within the cylindrical extension.When the shaft rotates,these blades create a pumping action,which forces the limestone and water into the grinding media bed.
Generally,attrition mills use media ranging in size from 3mm to 10mm.However,in the wet FGD application,the mill design was altered to incorporate 12.7mm through-hardened carbon steel balls.The specialized mill design allows the 6mm(1/4”) feed size of the limestone.Attrition arm tip speed is approxi- mately 270 m/min
After the limestone and water slurry has passed through the grinding media bed, the ground limestone slurry overflows and discharges from the top of the mill into a separation tank. A low speed mixer is incorporated into the separation tank, which allows the fines to continuously overflow to the mill product tank while coarse limestone particles settle to the bottom. A mill recirculation pump then carries the coarse limestone particles back to the mill to be re-ground.
The power consumption of these high efficiency attrition mills is relatively low. For example, a mill equipped with a 150 hp mill motor produced 9.75 metric tonnes per hour of 95% minus 325 mesh limestone slurry product when fed with 1/4” x 0” stone feed size. This equates to a specific energy based on the mill installed motor power of only 10.4 kWh per short ton of material processed.