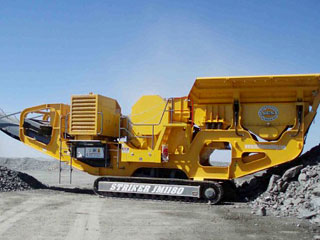
Comparison of Ore Hardness Measurements
As part of the ongoing project development for the Tenke Fungurume Copper-Cobalt Project in the Democratic Republic of Congo, Phelps Dodge Corporation has examined methodologies for determining the size of grinding mills to support a 7000 mtpd operation. Six samples were tested by Hazen Research, Inc. (HRI) to obtain the JK parameters using the JK Drop Weight Test, standard Bond crushing, and rod mill work indices, abrasion indices and by Dawson for Bond Ball Mill Work Index tests using crushed feed, and Standard Autogenous Grinding Design (SAGDesign) Tests, patented by Outokumpu. (See reference 8 below).
The comparison of these results gives context to how the various measurements relate to each other and how they can be used to obtain an accurate design for the grinding mills required for the Tenke Project. This is the first published direct comparison between JK Drop Weight, standard bond work indices, and SAGDesign test results. The SAGDesign test includes a SAG test followed by a Bond BM Wi test done on SAG ground material.
INTRODUCTION
After the presentation of the paper “SAGDesign Testing – What It Is and Why It Works” at the recently concluded SAG 2006 Conference in Vancouver, a question was asked about how SAGDesign ore hardness measurements compared with other comminution tests, specifically the JK Drop Weight Test and the parameters that are derived from such testing. At that time it was noted that a paper was being prepared for the CMP Conference in January to show how various ore hardness measurements compare with each other when done on the same samples.
This paper will therefore present the first such comparison using test results from the Phelps Dodge Tenke Fungurume Project where six composite samples were examined by the tests noted below. A seventh sample was tested at Dawson but not at other labs. The tests were done at four different laboratories listed below and included the tests shown.
Hazen Research, Inc.
- Bond Rod Mill Work Index
- Bond Abrasion
- Specific Gravity, 2 methods
- JK Drop Weight Tests – Data Analyzed by Contract Support Services, Inc.
Phillips Enterprises, LLC
- Bond Impact Crushing Work Index
- Specific Gravity
Advanced Terra Testing, Inc. (ATT)
- Unconfined Compressive Strength ASTM D 5731
- Specific Gravity, ASTM D 854
Dawson Metallurgical Laboratories, Inc.
- SAGDesign (SAG to T80 12 M followed by Bond BM Wi on SAG ground ore)
- Bond Ball Mill Work Index (Crushed Feed)
- Specific Gravity (part of the SAGDesign test).
The results from this work are presented below and are discussed in this paper. The SAGDesign results were compared to JK Drop Weight analysis of results by analyzing the SAGDesign Database for all tests done to date for SAG Pinion Energy (to T80 1.7 mm) and Bond Work Index on SAG ground ore. To data 63 SAGDesign tests have been done and this allowed the Tenke results to be ranked with respect to all the samples tested to date.
Critical issues with regard to the various tests done are reproducibility of the test result in duplicate tests, and the deliverable from the test. As far as the SAG portion of the SAGDesign test is concerned, it was the only SAG test done that had as a deliverable, the unit SAG pinion energy required which in this case was to grind the ore represented by the samples, from a feed size F80 of 152 mm to 80% passing 1.7 mm, and a simple adjustment procedure in case the SAG product size needed to be adjusted. Bond rod and ball mill work indices are readily converted to pinion energy for rod and ball mills but not for SAG mills.
Reproducibility, while not studied in this paper is clearly a part of the meaningfulness of the data presented. It was clear from the data that there are large variances between the various results that stem from the imprecision of the test measurement and/or the selection of the sample tested…
CONCLUSIONS
Considering the databases involved in comparing JKSimMet and SAGDesign results, both methods gave results in the same comparative range, that is, that the Tenke ore samples were among the 10% softest of all ore samples tested to date.
From the above and the correlation with other hardness measurements it is therefore concluded that the SAGDesign tests correctly identified the real grinding hardness of the ore samples tested.
Based on the shape of the SAG pinion energy versus frequency graph in Fig. 2, the SAGDesign test is measuring much more that just the impact breakage energy. It measures design energy.
Impact breakage energy is not the main factor in selecting power required for SAG grinding. It is well known that the combination of impact breakage and abrasion energy is needed.
In SAG Mill design often there is too much emphasis placed on Drop Weight tests. In most cases the provision of required impact breakage is a secondary result of providing enough total power to grind an ore. Controlling the ball size and ball charge level usually provides for the impact breakage.
The lack of reproducibility in comminution test measurements is a problem that demands many more measurements. The best and most cost effective way is to use the most accurate test.
The SAGDesign Test is such a test and does a good job of measuring required SAG pinion energy level and the Bond ball mill work index. (See reference 8 below).
High testwork costs and lack of samples for testing have, and will in the future discourage the use of more samples and ‘usual’ grinding tests, especially for small mining companies.
The Bond Rod Mill work indices were much higher than the Bond Ball Mill work index values. Because the ores were so soft, the effect of these Bond RM Wi results on required SAG grinding energy should probably be ignored for the Tenke project.
The use of Bond equations to calculate pinion energies in ranges where the mill feed size exceeds normal rod mill feed is a mistake and leads to lower than required SAG pinion energy. Fred Bond did not envision the use of these equations for other sizes than he had data to support.
A common problem here is that using former technologies, a client’s design engineer cannot accurately design a SAG mill from basic measured parameters.
Judging by the number of design errors that have been made in the last ten years alone is reason enough to state that a more fundamental approach is required for SAG mill design.
It is important that we all understand the fundamentals of SAG mill design. Otherwise mistakes will continue to happen.