Introduction
Many cement plants use coal and pet coke as the main fuel for the kiln to reduce their energy cost. Normally coke and coal contain sulfur and moisture in varying quantities. These fuels usually to go through a mill to obtain the right particle size and then need to get dried, usually with the hot gases from the kiln. Finally end the gases are filtered in a baghouse before discharging to the atmosphere.
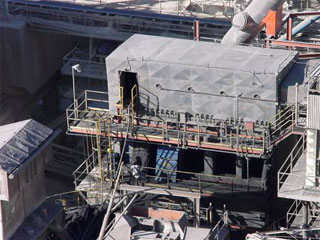
Corroding Coke Mill Baghouse
Due to the combination of hot acid components and condensing moisture, the corrosion inside a coal mill baghouse can be extremely severe. This affects the filter performance, increases the maintenance cost and can result in explosion hazard if air leaks in where corrosion has punctured the filter shell.
Many conventional coatings have failed in this demanding service forcing users to consider the use of expensive stainless alloys for the construction. Recently 3L&T developed a new type of polymeric coating called FlueGard™-225 capable of handling these hot flue gases in many industrial applications.
Cemex Ensenada
Cemex installed half a year ago a new coke mill, at their Ensenada plant in Baja California Mexico, including a new baghouse supplied by American Air Filter (AAF). Figure 1 Shows the location of the filter.
The plant uses pet coke from Petroleos Mexicanos, with an average sulfur content of 5.5% and around 10% of moisture.
Few months after the start of the equipment, plant personnel noticed signs of corrosion on the walls and ceiling of the clean gas plenum, the epoxy based original coating material was delaminating and failing. After six months the corrosion progress was alarming, at that point the project engineering team decided to install a better solution. Figure 2 illustrates the corrosion damage.
The plant contacted AAF and they recommended installing the FlueGard™-225 coating, they asked Solé S.A., the local partner for 3L&T, to review the filter and prepare a proposal to solve the corrosion issues.
FlueGard™-225 Application
The coating application was done during a plant shutdown late September 2004. Since the job requires complete access to the walls and internal structure, all the bags were removed. Figure 3 shows the bag removal in progress.
The walls, ceiling, tube sheet and hopper were sandblasted, using a coarse copper slag to a > 75μ profile ( 3 mils ), the Figure 4 shows the condition of the clean surface. The FlueGard™-225 was applied in two layers, using a conventional spray equipment, to a total dry film of 0.5 mm ( 20 mils ), Figure 5 shows the application in progress. The coating dries after 24 hours to an elastomeric, dry to touch film. At this time the new coating was inspected and approved.
The final stage for the full operating performance of the FlueGard™-225 protection, is a high temperature cure. This part of the process was done using the hot gases from four external burners. The inlet temperature to the filter was ramped up at a rate of 30ºC /hr. to a final cure temperature of 134ºC, which was maintained for 11 hours. At this point the coating is fully functional and provides an outstanding corrosion protection in this very harsh environment.
Other Applications
The Cemex Ensenada is just the latest application of the FlueGard™-225 in coal mill baghouses, so far there are multiple plants in the USA, Mexico, Italy and Romania that have benefited from this new technology.
Additionally, similar corrosion protection has been obtained in kiln baghouses, alkali bypass filters, ducts, fans and stacks that handle hot corrosive gases in cement and lime plants, power generation, oil refineries and waste incineration.
Conclusions The total cost of corrosion in a cement plant can be in the order of $500,000 per year, this includes not just the direct cost of maintenance but also indirect cost such as reduced production and fines for contamination.
The best way to protect the air pollution control equipments is using a proven technology capable of handling the high temperature, acid condensation and severe abrasion inside the filters and related equipment.
It is never too late to install the correct protection, but the best moment and the most cost effective, is on new equipment, before it is installed in place.