Gulin® is a professional manufacturer of agitated ball mill in China, We can provide you mining equipment with high quality. Stone crusher: jaw crusher, cone crusher, impact crusher, mobile crusher; Grinding mills: ball mill, raymond mill, vertical mill, hammer mill, ect. They have been exported to America, Italy, Turkey, Australia, Singapore, Indonesia, Vietnam, Iran, India, Chile, Venezuela, Libya, Ethiopia, United Arab Emirates, Kazakstan, Kyrgyzstan and receive high popularity. We believe Gulin® will develop with the world, we will make greater contributions to prosperity of the world.
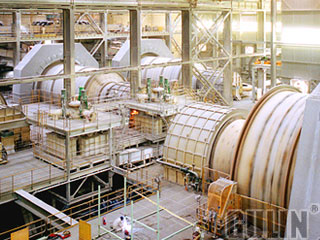
Agitated Ball Mill
Agitated Ball Mill
Most of the agitated media mills are used for slurries, only a minority is in industrial use for the fine grinding of dry powders. The grinding energy is transferred into the media by agitation with a rotating stirrer. Also combined agitation by stirrer and rotating body is known. The grinding chamber arrangement and shaft direction is vertical and there are three basically different mill types. The so called tower-mill has a screw-type rotor which lifts the grinding media and actually uses the gravity as driving force for media motion. This mill cannot be operated with very small media.
Second type is an agitated media mill with stationary grinding media filling; material transport is done by gravity or pneumatically. The third type is operated with a circulating media filling; material and powder are flowing through the agitated mill chamber. These two types of dry agitated media mills create high kinetic forces on the media and can be used with very small ball sizes. The grinding mechanism can be influenced by variation of the agitator speed and the ratio of media filling. High rotation speed and low media filling level effect a tendency to impact stress, whereas a high filling ratio of beads shifts the mechanism more to shear stress. In contrast to agitated wet ball mills, dry ball mills are typically low speed mills with predominant shear grinding.
Agitated ball mill grinding flow process
At the critical speed, the balls are centrifuged to the drum walls and the grinding effect gets lost. Typical rotation speeds are in the range of 60 – 80 % of the critical speed. A high speed level effects a cataract-motion of the balls, which has a high portion of impact stress. The grinding mechanism shifts to a higher portion of shear stress if the mill rotates slower and the motion changes to a cascade-type.
Gravity is the driving force to move the grinding media in ball mills. The mill body usually is a slowly rotating cylindrical or conical drum in horizontal arrangement. Mill dimensions reach up to 25 meters length (tube mills) and 13 meters diameter (SAG mills). The mill drum is wear protected with hard steel or ceramic liners. The same materials are used for the grinding media, which usually have a size of 20 – 100 mm. Some ball mills for very fine mineral products can be operated with relatively small media in the range of 10 – 12 mm. Tests with even Gravity is the driving force to move the grinding media in ball mills. The mill body usually is a slowly rotating cylindrical or conical drum in horizontal arrangement. Mill dimensions reach up to 25 meters length (tube mills) and 13 meters diameter (SAG mills). The mill drum is wear protected with hard steel or ceramic liners. The same materials are used for the grinding media, which usually have a size of 20 – 100 mm. Some ball mills for very fine mineral products can be operated with relatively small media in the range of 10 – 12 mm. Tests with even smaller balls show, that there is a limit in the stress intensity at 4 – 6 mm media size. Grinding of coarser particles is not possible anymore. And, if the balls are too small, they do not have enough energy to destroy the layers of fine particles sticking at the drum walls and at the media surface.