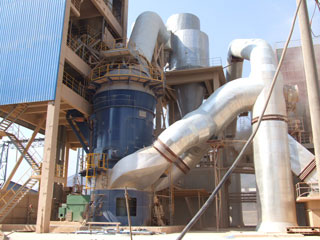
Vertical roller mill
Coal pulverizer is flexible design coal milling equipment also named coal mill. We absorb the advantages of Loesche coal mill and add some features too. Coal pulverizer can handle all grades of coal and is highly economical in terms of specific energy consumption.
Gulin coal pulverizer can grind all grade coal from hard coal, woody lignite, lignite to anthracite coal, petroleum coke, and besides this Gulin can supply a turnkey project including coal pulverizer design, coal pulverizer install, and coal pulverizer debug all kinds of coal grinding plants.
Coal Pulverizer used in Power PLant
Coal is pulverized (powdered) to increase its surface exposure thus permitting rapid combustion. Efficient use of coal depends greatly on the combustion process employed. For large scale generation of energy the efficient method of burning coal is confined still to pulverized coal combustion. The pulverized coal is obtained by grinding the raw coal in pulverising mills. The various pulverising mills used are as follows:
- Ball mill
- Hammer mill
- Ball and race mill
- Bowl mill also called roller-race mills or vertical spindle mills
The essential functions of pulverising mills are as follows:
- Drying of the coal
- Grinding
- Separation of particles of the desired size.
Proper drying of raw coal which may contain moisture is necessary for effective grinding.
The coal pulverising mills reduce coal to powder form by three actions as follows:
- Impact
- Attrition (abrasion)
- Crushing.
Most of the mills use all the above mentioned all the three actions in varying degrees. In impact type mills hammers break the coal into smaller pieces whereas in attrition type the coal pieces which rub against each other or metal surfaces to disintegrate. In crushing type mills coal caught between metal rolling surfaces gets broken into pieces. The crushing mills use steel balls in a container. These balls act as crushing elements.
BALL MILL (Ball Tube Mills)
Ball tube mills are rotating horizontal cylinders containing steel or special alloy balls. Coal intermingled with the balls is crushed by the impact and grinding action of the balls as the mill rotates. Hot air flowing through the ball mill carries coal particles to classifiers situated at both ends of the mill. Large particles rejected in the classifiers are returned to the grinding zone for further size reduction. Small particles passing through the classifier exit the mill through piping leading to burners in direct fired systems and to cyclone collectors in indirect fired (storage bin) systems.
It consists of a slowly rotating drum which is partly filled with steel balls. Raw coal from feeders is supplied to the classifiers from where it moves to the drum by means of a screw conveyor.
As the drum rotates the coal gets pulverized due to the combined impact between coal and steel balls. Hot air is introduced into the drum. The powdered coal is picked up by the air and the coal air mixture enters the classifiers, where sharp changes in the direction of the mixture throw out the oversized coal particles. The over-sized particles are returned to the drum. The coal air mixture from the classifier moves to the exhauster fan and then it is supplied to the burners.
BALL AND RACE MILL
ball and race mill is shown in fig. In this mill the coal passes between the rotating elements again and again until it has been pulverized to desired degree of fineness. The coal is crushed between two moving surfaces namely balls and races. The upper stationary race and lower rotating race driven by a worm and gear hold the balls between them. The raw coal supplied falls on the inner side of the races. The moving balls and races catch coal between them to crush it to a powder. The necessary force needed for crushing is applied with the help of springs. The hot air supplied picks up the coal dust as it flows between the balls and races, and then enters the classifier. Where oversized coal particles are returned for further grinding, where as the coal particles of required size are discharged from the top of classifier.
In this mill coal is pulverized by a combination of’ crushing, impact and attrition between the grinding surfaces. The advantages of this mill are as follows :
- Lower capital cost
- Lower power consumption
- Lower space required
- Lower weight.
However in this mill there is greater wear as compared to other pulverizes.
The use of pulverized coal has now become the standard method of firing in the large boilers. The pulverized coal burns with some advantages that result in economic and flexible operation of steam boilers.
Preparation of pulverized fuel with an intermediate bunker is shown in Fig. 4.22. The fuel moves to the automatic balance and then to the feeder and ball mill through which hot air is blown. It dries the pulverized coal and carries it from the mill to separator.
The air fed to the ball mill is heated in the air heater. In the separator dust (fine pulverized coal) is separated from large coal particles which are returned to the ball mill for regrinding. The dust moves to the cyclone. Most of the dust (about 90%) from cyclone moves to bunker. The remaining dust is mixed with air and fed to the burner.
Coal is generally ground in low speed ball tube mill. It is filled to 20-35% of its volume. Withsteel balls having diameter varying from 30-60 mm. The steel balls crush and ground the lumps of coal. The average speed of rotation of tube or drum is about 18-20 r.p.m.
Advantages
The advantages of using pulverized coal are as follows :
- 1. It becomes easy to burn wide variety of coal. Low grade coal can be burnt easily.
- 2. Powdered coal has more heating surface area. They permits rapids and high rates of combustion.
- 3. Pulverized coal firing requires low percentage of excess air.
- 4. By using pulverized coal, rate of combustion can be adjusted easily to meet the varying load.
- 5. The system is free from clinker troubles.
- 6. It can utilize highly preheated air (of the order of 700°F) successfully which promotes rapid flame propagation.
- 7. As the fuel pulverising equipment is located outside the furnace, therefore it can be repaired without cooling the unit down.
- 8. High temperature can be produced in furnace.
SHAFT MILL
Fig shows fuel pulverization with a shaft mill. The fuel from bunker is moved to feeder via automatic balance. Then from duct fuel goes to mill where it is crushed by beaters secured on the spindle of the mill rotor.
The pulverised fuel is dried up and then blown into shaft by hot air. Secondary air is delivered into the furnace through holes to burn the fuel completely.
Hammer mills:
In the feed processing process there may be a number of ingredients that require some form of processing. These feed ingredients include coarse cereal grains, corn which require particle size reduction which will improve the performance of the ingredient and increase the nutritive value. There are a many ways to achieve this particle size reduction, here we are looking at using hammer-mills, for information on roller mills, see the related links at the bottom of this page.
Both hammering and rolling can achieve the desired result of achieving adequately ground ingredients, but other factors also need to be looked at before choosing the suitable method to grind. Excessive size reduction can lead to wasted electrical energy, unnecessary wear on mechanical equipment and possible digestive problems in livestock and poultry. For more in depth information regarding what actually occurs to the ingredients during size reduction please refer to this link: particle size reduction.
Advantages:
- are able to produce a wide range of particle sizes
- work with any friable material and fibre
- ease of use
- lower initial investment when compared with a roller mill
- minimal maintenance needed
- particles produced using a hammermill will generally be spherical, with a surface that appears polished.