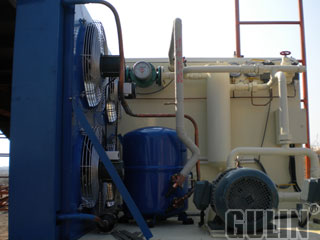
Air Classifier
Gulin® has manufactured a wide assortment of air classifier for air classification plant. One of the best high quality raw supplies are used in fabricating these high performance and durable machines. Utilized in various industries like mineral, steel, cement and ceramics for applications for example micro particle size, serrated liners and distinctive multi-tip rotor create many air-whirls, turbulence and aids in progressive grinding. Accessible in array of specifications, these may be customized as per client’s needs.
Air Classifier Used with Ball Mill
An approach to quantifying the impact grinding performance of different materials is presented. Based on a dimensional analysis and on fracture mechanical considerations, various materials are over a wide size range. Different polymers, crystalline substances, glass and limestone can be characterised quantitatively. The derived material parameters are applied to the systematic modelling of grinding in impact mills. A population balance model is presented and the results of the simulation for an air classifier mill are shown. The developed model permits a clear separation of the influence of material properties, mill-specific features and operating conditions, thus enabling a deeper understanding of the grinding process.
Lower Primary grinding cost as in the present grinding system could be decreased as rather than grinding 500 mesh only 300 mesh grinding could be required for feeding to the Ball Mill. Also the production would be greater.
Overall production price per MT would go down, because of less initial grinding necessary in present technique, much more percentage of fines getting generated in the Ball Mill and minimization of coarse generation.
In case of item blending/coating, with Ball Mill more homogeneous and consistent mixing is achieved compared to conventional grinding/mixing technique.
On the effect of grinding process
Every material performs differently in the milling process and exhibits different grinding characteristics. A systematic and quantitative characterisation of the grinding performance of a powder is currently beyond scope because both the stressing of the particles in a mill and the breakage behaviour even under well-defined stressing conditions are not sufficiently understood, and the comparison of materials in a comminution process can therefore only be realised with the help of milling tests. These tests give results which are of value only for the type of mill under consideration. The possibility of transferring these results to other mills is debatable. This situation and the lack of understanding of the influence of material properties on the comminution process is totally unacceptable. In this paper, an approach which describes the grinding performance of different products independent of the mill properties is introduced.
Furthermore, the modelling of impact grinding processes is addressed. In order to operate a modern and flexible process, it is essential to be able to at least estimate the effect of changes to the operational parameters or products on the process result. Even with a statistically optimised experimental strategy, the required effort in time and cost for this purpose is still considerable. A systematic and physically reliable computer simulation of the process would be a fast and cheap alternative to overcome these problems. Furthermore, a realistic model can help to understand the milling process and the interaction of single process steps. An approach to the simulation of grinding mills based on a population balance model is presented. A simple model to describe the individual process steps inside the mill (i.e. grinding, classification and transport) was chosen. The main focus was on a clear separation between material and operational parameters, respectively, in order to investigate their influence on the comminution result separately.