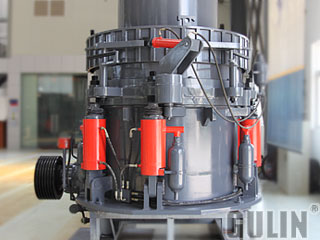
Tantalite Crusher
Tantalite is the most important mineral form of tantalum, a specialty metal used mainly in the electronics industry for the manufacture of capacitors and in several specialty alloy applications.
Tantalite crusher is an important tantalite processing machine, Gulin® is a professional manufacturer of tantalite ore crushing plant in China, and we export tantalite crusher machines to Zimbabwe, Kenya, Malaysia, Nigeria, South Africa, India, Pakistan, USA, UAE, and other countries.
Gulin® Tantalite Crushers
The tantalum may be the metal that acid resistance corrodes, for chemistry installment, surgical operation’s displaying bone stop plate and stitching, uses within the electron tube neutral tool steel.
According to the above application domain, must use mill arrive at the tantalite further grinding to offer the different pellet, need using tantalite mill, or other crushers. To the further mining process, it must make use of the tantalite mill, for example ball tantalite mill, MTW tantalite mill.
The entire tantalite crushing plant can produces some 7,000 tones each year of milled Industrial Grade tantalite for local and export sales, with using tantalite crusher and tantalite mill to complete whole tantalite crushing plant.
Tantalite Ore Crushing Process
For the industrial tantalum manufacture, the mining or blasted tantalite, ought to be loaded to tantalite production line by the heavy truck. In the first step, the tantalite ore should be transported into tantalite jaw crusher, impact crusher or gyratory cone crusher for the primary crusher by belt conveyor. Which crushing machine you choise based on the size of the tantalite. After tantalite crushing processing line and also the vibrating screen, how big tantalite less than 3 inch is going to be transported into tantalite vertical roller grinding mill or tantalite roller ball mill for grinding. The size of tantalite above 3 inch will be vibrating and recovery for that second crusher process by vibrating screen. The procedure is going to be going on before tantalite ore below 3 inch.
The beneficiation of tantalite ores usually involves preconcentration, primary concentration and concentrate clean up. The choice of any or all of these processes would depend on the nature of the ore, particularly the content of Ta2O5 in the ore relative to its associated minerals and impurities.
Typically, mechanically mined ores contain less than 0.1%Ta2O5, and would therefore essentially require enrichment through the three processes stated above. The concentration processes may be carried out by wet gravity, magnetic or electrostatic methods or by flotation to produce concentrates containing up to 70% combined Ta2O5 and Nb2O5 to meet extraction requirements. However, the universally employed method for the concentration of tantalite ores is gravity separation – the separation of two or more minerals as a result of differences in specific gravity and their movement in response to the force of gravity and one or more other forces. Other methods, when used, are employed in the final cleanup of gravity concentrates.