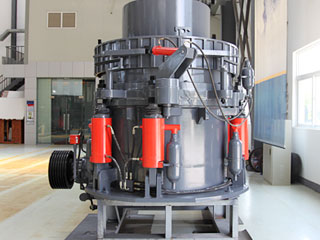
Hydraulic Cone Crusher
HPC cone crushers have been developed to crush feed materials into desired end products efficiently, reliably, and economically.
Gulin Mining and Construction Technology, the global leader in rock crushing technology, has developed the HPC cone crusher series to fulfill all crushing needs. Incorporating the latest crusher know-how, the HPC Series combines the highest crushing efficiency and end product quality with the lowest per ton production costs.
Take a closer look at the HPC Series crushers. You will be sure to find a HPC cone crusher ideally suited to your needs.
Hydraulic cone crusher application
- Metallurgy industry: Hydraulic cone crusher usually is widely applied as crushing equipments in primary or secondary stages.
- Construction and mining industry: Hydraulic cone crusher is suitable for crushing of many kinds rocks such as concrete, fireproof materials, bauxite, quartzite, corundum, perlite, ironstone, basalt, sand, gravel, other ores etc.
- Building materials, chemicals, transportation, etc.
Hydraulic cone crusher features
- High crushing ratio and high efficiency: Hydraulic cone crusher with high related power and movable cone diameter can improve the efficiency.
- Hydraulic cone crusher protecting methods: This cone crusher adopts three protecting equipments such as protecting oilcan, locking oilcan and hydraulic driving oilcan.
- Less consumption of wearing parts and low operating costs: Hydraulic cone crusher is used in large stone quarries can solve many problems of impact crusher such as small crushing ratio, energy consumption, impact plates wearing faster etc.
- Crushing chamber specially designed can sharply increase the crushing ratio, output and content percentage of cubical products in final crushed materials.
- The concave and mantle made by high manganese steel and the abrasion of cone crusher is reduced greatly and can last long compared with old cone crushers.
- Hydraulic cone crusher consists of hopper, cone head, concaves, mantle, movable cone, eccentric bearing bushing, sealing gasket, slab, gear, friction plate, small gear, housing, oil sealing, bowl liner, movable bushing, guard plate etc.
Hydraulic Cone crusher specification
Model | Cavity (coarse/fine) | Discharge setting min.(mm) | Feed opening (mm) | Capacity (t/h) | Power (kw) | Weight (t) | movable cone diameter (mm) |
---|---|---|---|---|---|---|---|
HPC-160 | C | 13 | 150 | 120-240 | 160 | 13 | 950 |
F | 6 | 76 | 55-180 | ||||
HPC-220 | C | 13 | 225 | 150-430 | 220 | 18 | 1160 |
F | 6 | 86 | 90-260 | ||||
HPC-315 | C | 13 | 290 | 190-610 | 315 | 26 | 1400 |
F | 6 | 100 | 108-320 | ||||
HPC-400 | C | 13 | 320 | 230-700 | 400 | 33 | 1500 |
F | 6 | 110 | 145-430 |
Total control of crusher and process
Advanced automation
Automation is playing an increasing role in the development of crushing processes today. The IC50 automation unit comes as standard in most HPC Series cone crushers. This contributes significantly to the efficiency and availability of the crusher. The IC50 automation unit guarantees constant choke feeding. It also improves the liner utilization rate and thus the end product quality by promoting inter-particle crushing. The automation system keeps crushing at maximum operational limits and within safety margins. The IC50 also records production information and crusher performance. It gives graphic trending of up to 24 hours of operation, which improves reporting capabilities. Automation makes it possible to perform analyses and corrective actions based on process variations, and to decrease the need for wear part calibration.
Friendly for the operator
Advanced automation, easy adjustment, and a limited number of maintenance points make the HPC Series particularly operator friendly. The automation system aids the operator in finding the right crusher settings quickly and easily. Less operator observation during crushing is required. Hydraulic adjustment of the crusher is safe and fast, and can be performed continuously under crushing load. For service, HPC cone crushers can be dismantled completely from above. Changing the liners does not require backing materials thanks to the machined wear parts. A pressurized sealing system keeps the crusher cleaner, resulting in longer filter change intervals and more reliable crusher operation.